The bolt carrier group is the heart of the AR-15. It’s the primary mover of the rifle: the part that does the cycling, the feeding, the case extraction. It’s the part that bears the brunt of the blast from the gas system and takes the greatest beating from the buffer system.
With all of that riding on your AR-15 BCG, it’s essential that you equip yourself with the best one possible; but which one is the best? With a myriad of different designs, coatings, materials, and more on the market, it can feel impossible to sort through them all to find the right one for you.
Below, we’ll break down the different components of a bolt carrier group, review the various coatings available, and take a look at some of the most popular models currently on the market.
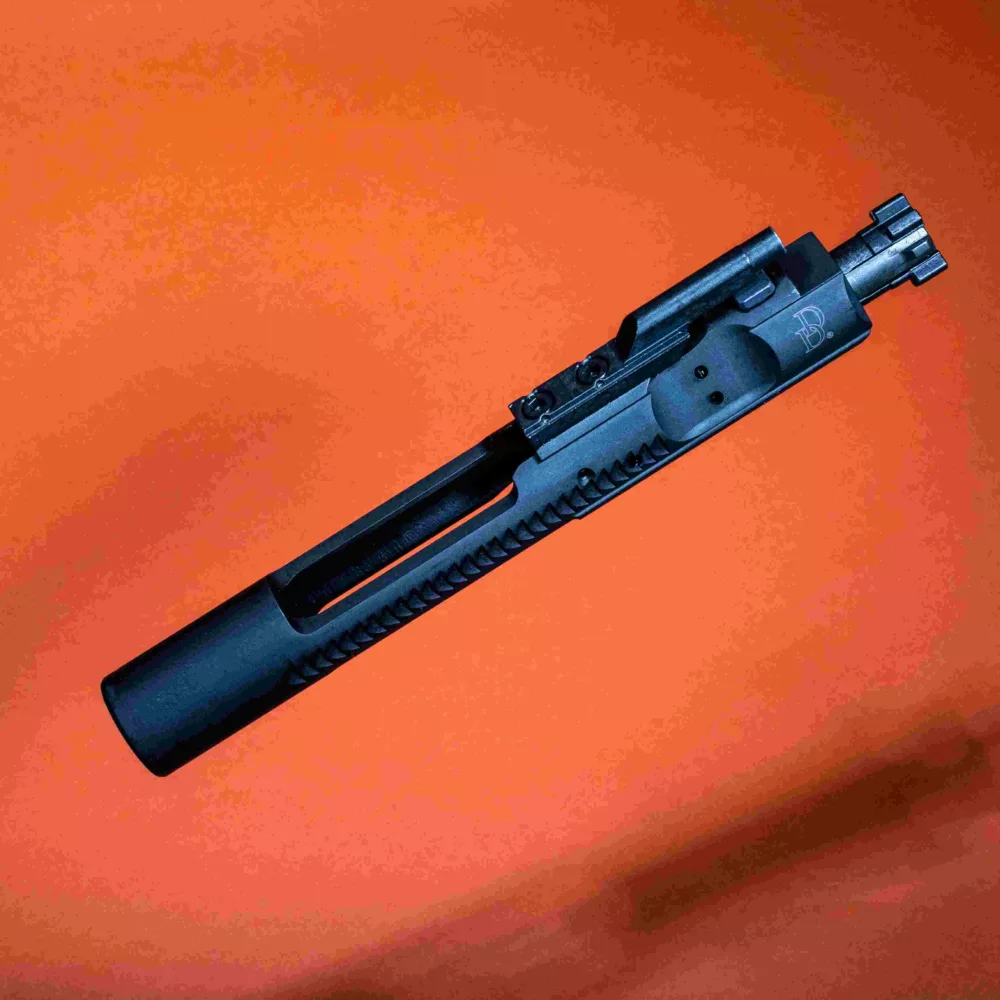
What is a Bolt Carrier Group (BCG)?
A bolt carrier group or BCG is a collection of parts that work together to help your rifle cycle ammunition, including loading new rounds into the chamber, igniting the round, and extracting the spent brass casing after the round has been fired.
The primary components of the BCG are the carrier itself, the bolt, and the firing pin. The BCG also contains several smaller parts, including the gas key, cam pin, firing pin retaining pin, ejector, and extractor with its related springs and retainer.
Overview of BCG Terminology
While BCGs are largely standardized (you can drop nearly any AR-15 bolt carrier group into nearly any AR-15 rifle), there are still many differences in the way they are made, the materials that are used, and the standards to which they are held. Often, these are expressed as acronyms with little explanation as to what they mean or how they affect the BCG’s performance.
For instance, many bolt carrier groups are advertised as being MPI tested. This stands for Magnetic Particle Inspected, a non-destructive testing process that involves magnetizing the part in question and exposing it to a dust or slurry of ferromagnetic particles to detect cracks or aberrations in the steel.
MPI testing allows for microscopic or otherwise undetectable imperfections in the bolt carrier group to be detected, ensuring a very high degree of quality in the finished product. This type of testing can be done to random samples from a lot or batch, or applied to each individual part.
High-pressure testing is a similar process used to evaluate the strength of a BCG. The testing process is largely self-explanatory; the bolt carrier group is exposed to extremely high pressures, simulating the pressure of a fired cartridge, and then examined for cracks or deformation. While not technically destructive, this type of testing is usually conducted on a few randomly chosen units from a lot rather than on an individual basis.
You may also find bolt carrier groups listed as “Semi-Auto-Rated” or “Full-Auto-Rated”. There’s some confusion about these terms, but the difference is actually quite simple.
Full-auto-rated BCGs have a longer lug at the rear section of the carrier, which is necessary to properly interface with an automatic fire control group. Semi-auto-only carriers have a smaller lug. In some cases, particularly with fast rates of fire or demanding firing schedules, full-auto-rated bolt carriers may offer greater longevity by merit of the extra material they carry.
Certain bolt carriers, typically marketed as “low-mass,” may have even more material removed than a standard semi-auto-rated bolt carrier group to reduce reciprocating weight and therefore recoil.
Lastly, many bolt carrier groups are designated as Mil-Spec, meaning that they conform to the U.S. Military’s standards for materials, coatings, manufacturing processes, and quality control. While Mil-Spec carriers can be very high quality, they may lack some more modern refinements, as Mil-Spec standards have not been updated for some time.
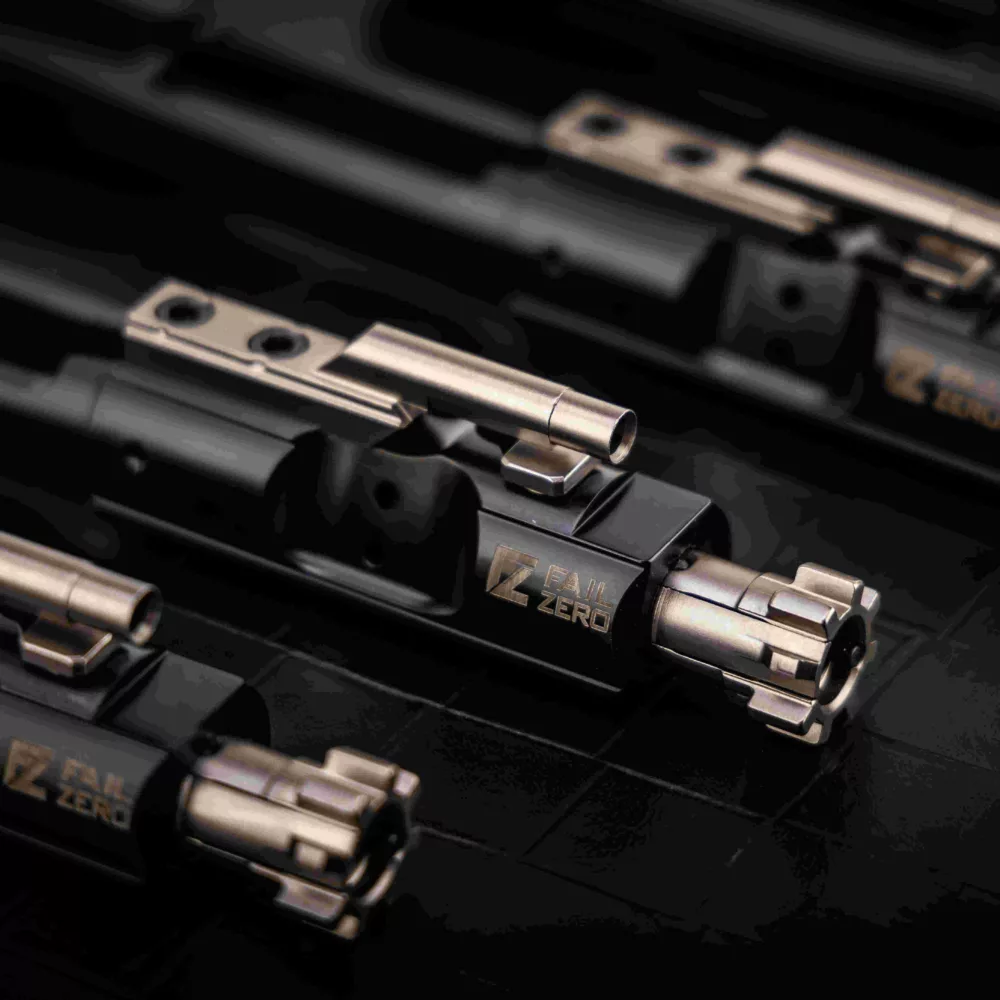
Bolt Carrier Group Finishes
For the most part, bolt carrier groups are manufactured with the same or similar materials and conform to a mostly standardized design. One of the primary places they diverge is in their coatings, of which there are several common options.
Phosphate
One of the oldest and most proven coatings is manganese-phosphate, also known as parkerizing. Parkerization creates a rough but durable surface on the metal which protects against corrosion. It’s among the most economical of bolt carrier group finishes, but is typically combined with chrome lining for certain high-wear locations, such as where the bolt slides against the inside of the carrier.
The rough surface of a parkerized bolt works in its favor to better retain oil or lubricant, but it also tends to adhere more strongly to carbon, making these types of bolt carriers more difficult to fully clean than other, slicker finishes.
Phosphate is the only truly Mil-Spec bolt carrier group finish, so rifle cloners need look no further than this option.
Nitride
Nitride is a more modern finish that uses a specialized heat-treating process to bond nitrogen to the surface of the steel. Unlike additive finishes, this process does not deposit or build up any kind of layer on the bolt carrier group; instead, it chemically alters the surface layer of the steel, adding no additional thickness or material.
The core advantage of non-additive finishes is that they are extremely resistant to damage or chipping; because both the surface material and the substrate are the same contiguous piece of steel, there is no weak point or joint to fail.
Nitriding creates an extremely hard, very smooth finish. It’s extremely corrosion and abrasion-resistant, and tends to resist carbon adhesion better than phosphate. However, the finishing process is more costly, so expect to pay a modest premium for nitride compared to some other finishes.
Nickle-Boron (NiB)
Nickle-Boron coatings, often abbreviated as NiB, are a type of additive coating prized for their low friction and ease of cleaning. Unlike the previous two finishes, this coating involves bonding a layer of nickel-boron to the underlying substrate to create a protective layer rather than altering the steel.
Because of this, it’s possible, albeit fairly rare, for the coating to delaminate. It’s most common in instances when the BCG suffers damage, such as being dropped onto a hard surface, or when the substrate was improperly prepared before coating, but the risk of the coating chipping or otherwise wearing away does discourage some users from choosing NiB bolt carrier groups.
However, the benefits of extreme corrosion resistance and very easy cleaning are still worthy of consideration.
Chrome
Chrome coatings are in most respects the same as nickel-boron; in both instances, a coating of corrosion-resistant metal is added to the bolt carrier group, protecting it from rust and increasing its lubricity.
The primary difference is that chrome coatings use a chrome alloy rather than a nickel-boron-based one, which creates a brighter, shinier finish. Chrome offers exceptional wear resistance in addition to its other beneficial properties, which is why this coating is often used for high-wear surfaces, such as the inside of the bolt carrier in parkerized BCGs or the chambered of many AR-15 barrels.
DLC
The last of our additive coatings, diamond-like carbon finishes (DLC) uses a process called physical vapor deposition (PVD) to build up a layer of carbon in a specific molecular structure on the surface of the bolt carrier. These coatings, despite being only a few microns thick, offer incredible wear resistance. Their hardness level is similar to that of diamond—hence the name.
DLC coatings offer the lowest possible level of friction, minimizing their need for lubricant and making the removal of built-up carbon nearly effortless. Like all additive coatings, though, they do come with a low risk of chipping from damage or improper application.
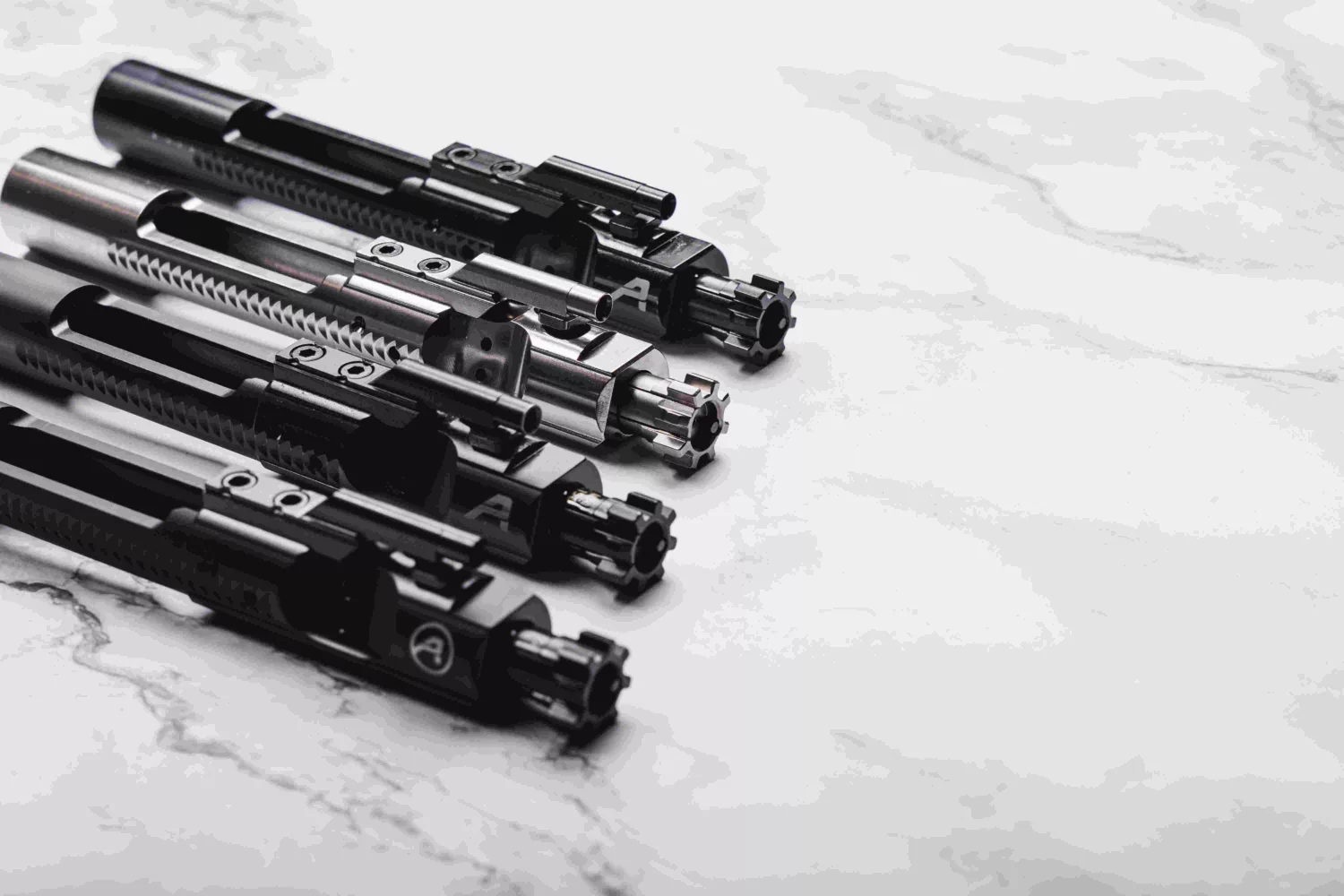
Top Manufacturers of AR-15 Bolt Carrier Groups
There are hundreds of bolt carrier groups on the market from dozens of manufacturers, making it impossible to pick a single best model or even a selection of them. Different designs, coatings, materials, and more make them each suited to a different purpose.
But, below we’ve curated a list of some of the more popular brands on the market.
BCM
Bravo Company Manufacturing is a staple of the AR-15 industry, long respected for its exceptional quality control and reasonable prices. They command a certain premium but thoroughly justify it with a spotless reputation for ruggedness and performance.
BCM offers both black bolt carrier groups with a Mil-Spec chrome/phosphate finish and flat-dark earth carriers finished with their Ionbond DLC. Their flat dark earth BCGs in particular are popular as a way to add an accent color to your AR-15 and for their unique coating, which is exceptionally smooth and wear-resistant.
Rubber City
Rubber City Armory offers a wide variety of bolt carriers, each with different materials, designs, and calibers, but all made with the same commitment to quality.
While they do offer a fairly standard BCG with a nitride finish, they also manufacture low-mass carriers, which have extraneous material removed to reduce reciprocating weight, and titanium carriers, which achieve the same result by using a lighter material. These bolt carriers are sometimes used in competition rifles as part of a system to reduce recoil and increase cyclical speed.
Perhaps their most innovative bolt carrier group, though, is their adjustable gas key BCG. This unique design allows the user to fine-tune their gas system using only a drop-in part, without having to install an adjustable gas block on their rifle.
Rubber City’s adjustable gas key makes tuning as simple as turning a few screws to control the flow of gas.
Aero Precision
One of the most recognizable names in the AR-15 industry, Aero Precision has built an ironclad reputation by providing quality rifles at approachable prices for decades. Their bolt carrier groups are no different, offering consistent performance and a range of finish options at a variety of price points.
In addition to their standard nitride, nickel-boron, and phosphate bolt carrier groups, Aero also offers a Pro BCG. The Pro model features improved materials, more sophisticated machining processes, and additional attention to fit and finish, resulting in a refined product perfect for demanding users.
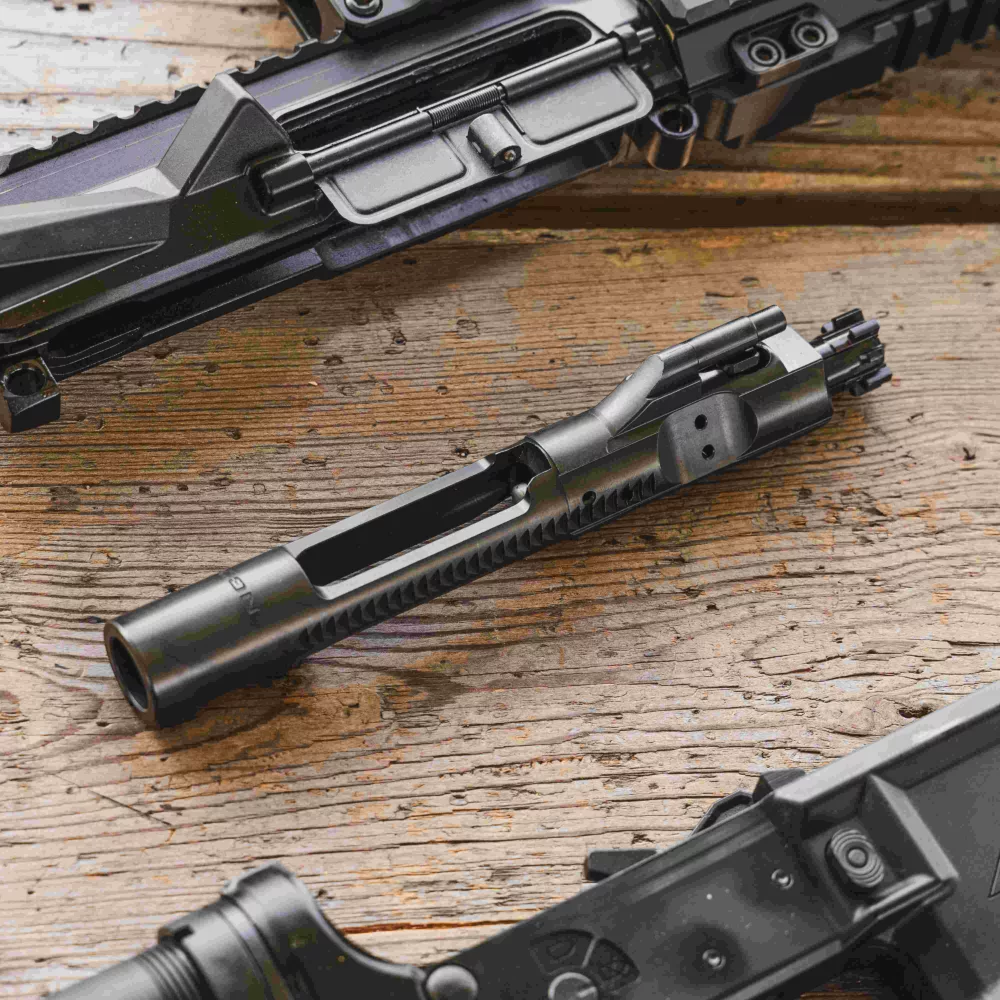
Does it Matter Which Bolt Carrier Group You Use?
For most users who use their rifle recreationally at the range, the choice of bolt carrier group is fairly straightforward. Simply choose your preferred BCG from a reputable manufacturer, and you’re likely to get reliable performance for many thousands of rounds. As long as you are mindful in your maintenance and use quality ammunition, you should have a suitably reliable rifle for recreational use.
Demanding users, on the other hand, such as those who use their rifles for duty or competition, ought to select their bolt carrier group more carefully. When the price of failure is high, it pays to invest in quality parts up front, and bolt carrier groups are no exception.
Conclusion
Bolt carrier groups come in a plethora of different designs and finishes, each tailored to a specific purpose. For casual or recreational use, these differences are negligible.
For serious use in the line of duty or for personal defense, though, it’s worthwhile to buy a little peace of mind by choosing the best bolt carrier possible.